Client Facts
UK Atomic Energy Authority (UKAEA), Harwell, Oxfordshire
Nuvia Group
Challenge
The Nuvia group was tasked to decommission the UKAEA site at Harwell in Oxfordshire and transform it into a world-class centre for excellence in science and innovation. As part of the overarching project, Nuvia was contracted to design and build a nuclear waste encapsulation facility at Harwell that could transport stainless steel drums containing intermediate-level radioactive waste (ILW) through the process.
Solution
Project partner ExMac Automation deployed a custom-built conveyor system designed to transport stainless steel drums containing ILW weighing up to 2000 kg through the process.
The drums, which are 800 mm in diameter, 1200 mm high and weighing up to 1000 kg, are loaded onto an ExMac conveyor system to be transported from an existing drum storage facility through each stage of a process that involves drum inspection and grout filling of the drums before conveying them back to an existing storage facility. During the process, the weight of the drums increases to a maximum of 2000 kg.
To meet Nuvia's specification required the contact surfaces of conveyors be stainless steel, ExMac designed a custom-built handling system consisting of sets of powered roller conveyors fitted with stainless steel tube rollers and side guides; cross-chain transfer units are fitted with stainless steel pads fixed to the chains. The rectangular conveyor system carries the steel drums inside a "cell’ with a concrete roof and walls. The support structure of the conveyors and any equipment not in contact with the drums were manufactured from carbon steel and finished with special paint.
Because the cell is located in a restricted area, ExMac also designed and supplied a drum removal system consisting of a hand-operated cable winch recovery bogie and hydraulic cylinder-driven drum pushers. In the event of a conveyor breakdown, the drum pushers are extended through the walls to push the steel drums into position where they can be conveyed to the storage facility.
Proving all components and the conveyor system off-site was a key requirement and determinant of the success of the project. ExMac was able to test the conveyor system offsite at its workshop and assemble accordingly. Each piece of equipment underwent a unit trial followed by a Full FAT and buy-off by both Nuvia and its end client the UKAEA.
Remarking on the success of the project and the collaborative venture, Andy Blue, Design Manager for Nuvia, comments, “ExMac Automation was involved in the project from the start, and the input of its design and engineering team on the conveying system was invaluable. The installation itself also went very smoothly and we were delighted with the result.
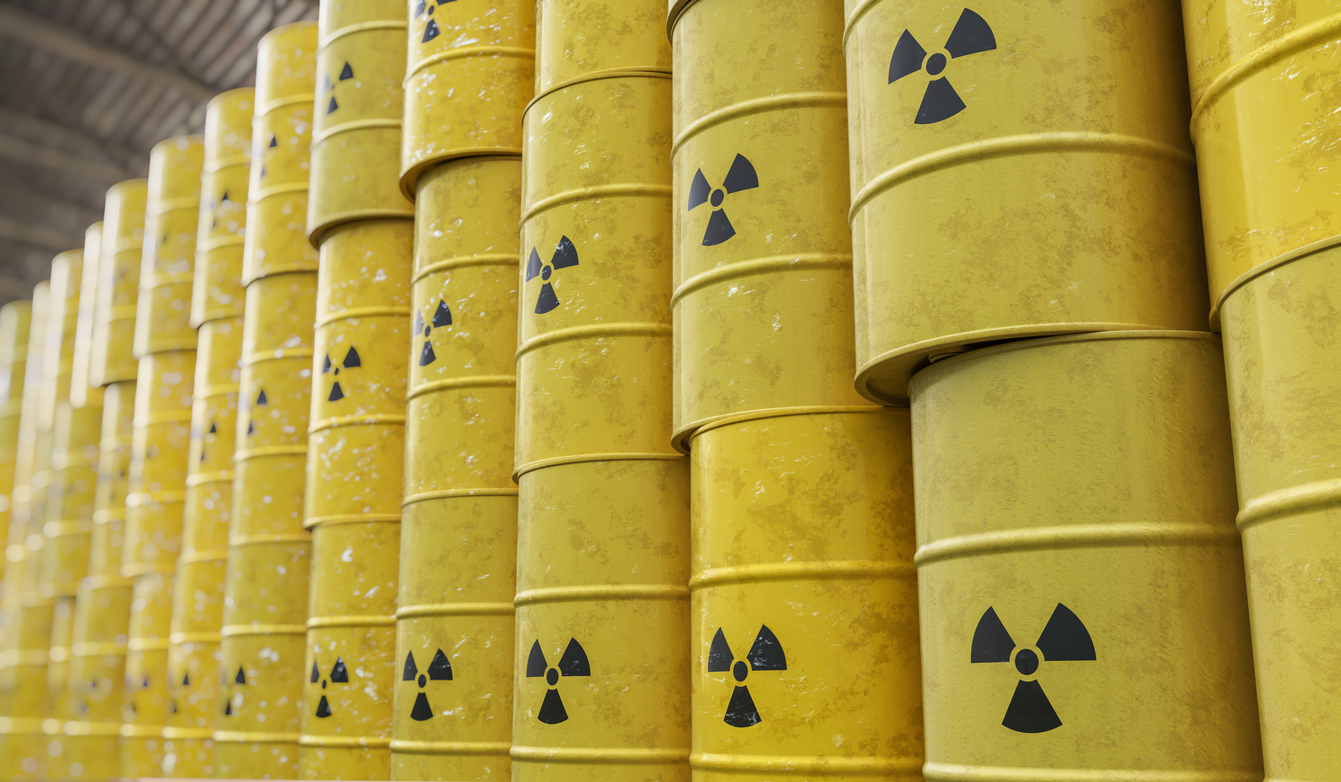